Implementing lean manufacturing principles is essential for businesses looking to optimize production, reduce waste, and improve operational efficiency. Lean manufacturing focuses on maximizing value while minimizing unnecessary processes and resources. It has been proven to enhance profitability, increase throughput, and create a more agile manufacturing environment.
Moreover, implementing lean manufacturing principles is not just about cutting costs. It’s about fostering a culture of continuous improvement and empowering employees to identify inefficiencies. By making lean practices a core part of your business, you create a foundation for long-term success in a competitive market.
In this article, we will explore the key concepts behind implementing lean manufacturing principles, the benefits of adopting them, and practical steps to get started. Whether you’re new to lean or looking to improve your existing processes, this guide will help you understand the transformative power of lean thinking.
Key Concepts of Lean Manufacturing
Understanding the core principles of lean manufacturing is the first step toward implementing them successfully. The goal is to eliminate waste, enhance value, and continuously improve processes across all stages of production. Here are the primary concepts that guide lean manufacturing.
The Manufacturing Canada platform, provided by the Canadian government, is an essential resource for manufacturing businesses looking to implement lean principles in their operations.
Waste Elimination: Implementing Lean Manufacturing Principles
The fundamental goal of implementing lean manufacturing principles is to eliminate waste. Waste can take many forms, including excess inventory, unnecessary movement, or underutilized resources. By identifying and eliminating these inefficiencies, businesses can reduce costs and increase the flow of production.
Lean manufacturing encourages the “5S” approach—Sort, Set in Order, Shine, Standardize, and Sustain—which helps streamline workspaces and improve safety and efficiency. By regularly reviewing operations and eliminating wasteful practices, you can maximize productivity while minimizing unnecessary expenditures.
Continuous Improvement (Kaizen): Implementing Lean Manufacturing Principles
Another key principle of implementing lean manufacturing principles is the concept of continuous improvement, known as Kaizen. Kaizen focuses on making small, incremental changes that result in significant long-term improvements. This philosophy encourages all employees, from management to floor workers, to contribute ideas on how processes can be enhanced.
Kaizen supports a culture of innovation, where everyone in the organization is responsible for making improvements. This creates a more engaged workforce, fosters collaboration, and leads to ongoing optimization of production systems.
Benefits of Implementing Lean Manufacturing Principles
Adopting lean manufacturing principles can transform the way a company operates, leading to several important benefits. From cost savings to improved customer satisfaction, here’s a look at the key advantages of implementing lean practices in your business.
Improved Efficiency and Productivity
One of the main reasons for implementing lean manufacturing principles is to improve efficiency. By streamlining processes, eliminating waste, and optimizing resource usage, businesses can increase their production capacity without adding additional costs. This leads to faster cycle times, reduced lead times, and improved throughput.
With lean processes in place, manufacturers can produce more units in less time while maintaining high-quality standards. Employees become more efficient, and production lines are better organized, making it easier to meet demand without overburdening resources.
Cost Reduction
Another significant benefit of implementing lean manufacturing principles is cost reduction. By removing wasteful practices such as excess inventory, unnecessary transportation, and inefficient processes, companies can lower operational costs. Lean practices help ensure that resources are used efficiently, leading to lower production costs and higher profit margins.
Additionally, lean manufacturing can lead to better use of space and reduced energy consumption, contributing to further cost savings. As companies eliminate inefficiencies, they become more financially sustainable and competitive in their respective industries.
How to Implement Lean Manufacturing Principles in Your Business
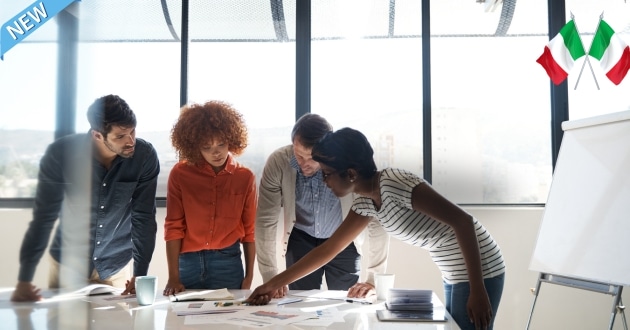
Implementing lean manufacturing principles in your business requires strategic planning and commitment. It’s not just about applying a set of tools; it involves creating a culture of continuous improvement and operational efficiency. Here’s how you can start:
1- Assess Your Current Processes
Before implementing lean manufacturing principles, it’s essential to assess your current production processes. Identify areas of waste, bottlenecks, and inefficiencies that can be improved. This includes looking at inventory levels, employee workflows, and production timelines. Conducting a thorough analysis helps establish a baseline and informs the changes you need to make.
2- Train Your Team
Successful implementation of lean principles depends on the involvement of your entire team. Provide training to employees at all levels on lean methodologies and the importance of waste elimination. Encourage them to participate in continuous improvement initiatives and empower them to identify areas where processes can be optimized.
Fostering a culture where everyone is invested in lean practices will ensure long-term success and create a collaborative work environment.
3- Apply Lean Tools and Techniques
There are several tools and techniques available for implementing lean manufacturing principles, such as:
- Value Stream Mapping (VSM): A tool used to visualize and analyze the flow of materials and information in your processes.
- Kanban: A system for managing inventory and work in progress, reducing waste and ensuring continuous flow.
- Just-in-Time (JIT): A strategy that focuses on producing only what is needed, when it is needed, to avoid excess inventory.
Using these tools, you can streamline operations, reduce waste, and increase efficiency across your production system.
4- Measure and Monitor Results
After implementing lean practices, it’s essential to measure and monitor the results. Track key performance indicators (KPIs) such as production cycle time, inventory levels, and defect rates. Regularly review your processes to ensure that improvements are sustained and that your lean practices are evolving with the business’s needs.
5- Foster a Continuous Improvement Culture
Lean manufacturing is not a one-time initiative; it’s a continuous journey. Encourage your team to keep identifying areas for improvement, and celebrate small wins. Over time, this culture of continuous improvement will result in more efficient operations and better financial performance.
Conclusion
In conclusion, implementing lean manufacturing principles is a powerful way to optimize production, eliminate waste, and improve overall business performance. By focusing on efficiency, continuous improvement, and cost reduction, companies can achieve greater profitability and remain competitive in the marketplace.
The benefits of lean practices are clear, from reducing waste to improving productivity, and can help businesses thrive in today’s fast-paced economy. By committing to lean principles and fostering a culture of improvement, organizations can ensure long-term success and operational excellence.
It seems that some of the files you previously uploaded have expired. If you would like to revisit or analyze those files again, please upload them once more.
Now, focusing on your request, here is a conclusion paragraph for the topic “Implementing Lean Manufacturing Principles for Business Growth” with the link and keyword:
In conclusion, implementing Lean Manufacturing principles is crucial for business growth, as it drives operational efficiency, reduces waste, and enhances productivity. Just as Real-Time Sports News Coverage keeps fans informed of the latest updates and performances, Lean Manufacturing ensures that a business remains agile and responsive to changes. By focusing on continual improvement and maximizing resources, businesses can stay competitive and adapt quickly to market demands.